The voind robot arm rotates on a axle that would originally sit on a pair of plain plastic bushings.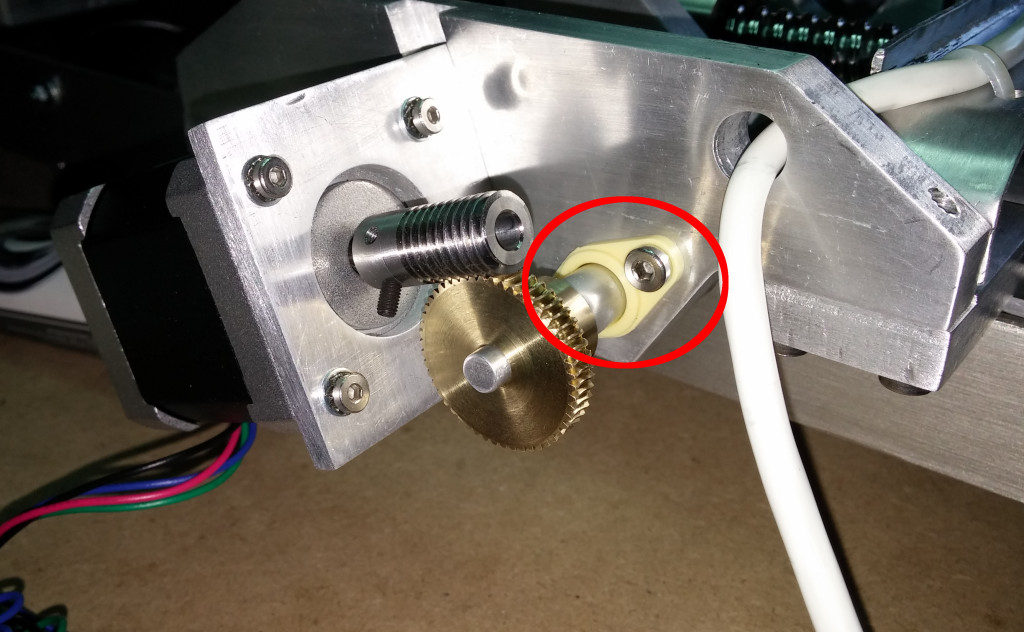
However, due to the lever effect of the arm’s weight pivoted on the rear bushing and the amount of play that these bushes naturally allow, this arrangement was causing noticeable play on the worm/wheel engagement which we feared would quickly wear out the gears. Additionally the lever effect was causing excessive load for the bushing which would cause further play.
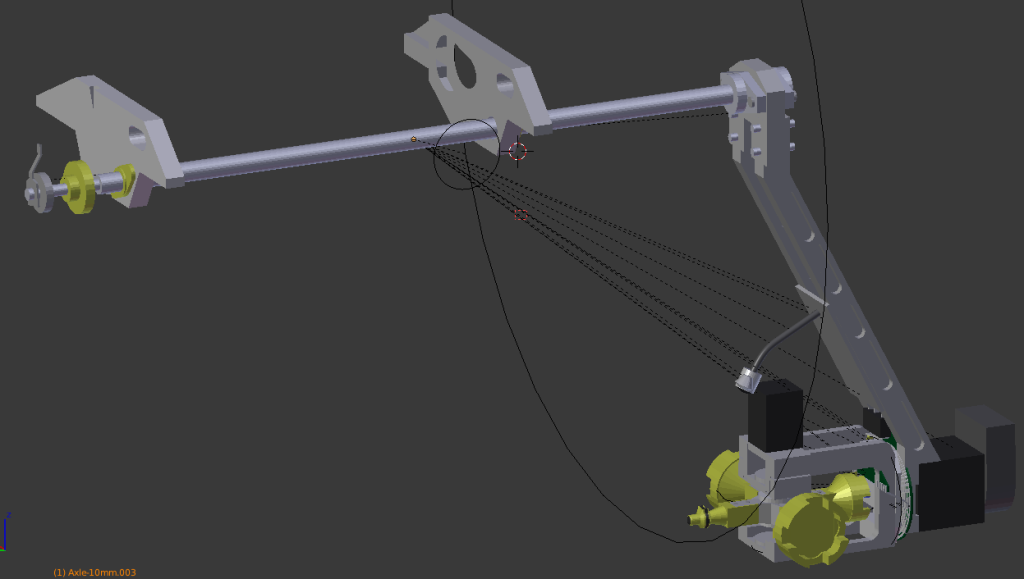
This problem was addressed by a) replacing the aluminum shaft with a steel one; b) replacing the plain plastic bushings with a pair of ball bearings;
Using bearings would help to counteract the loads, achieve a more stable support for the shaft and bring the shaft play under control. We also went for an arrangement with a needle bearing at the front where most of the load is applied and a ball bearing at the back close to the worm/wheel.
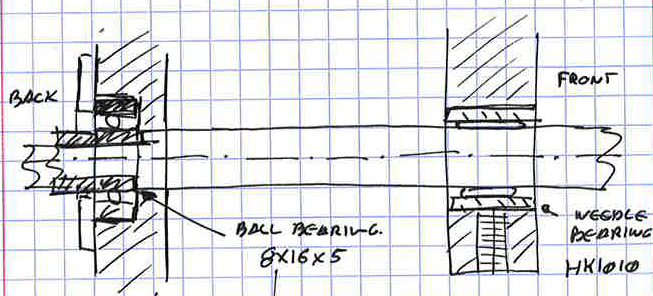
(bearings)
The first challenge was to rework the two aluminum parts to house the bearings. We also wanted to recycle the existing parts to save energy and time.
Fitting the needle bearing to the front part was simply a matter of enlarging the existing hole for 14mm, and using some sand paper to obtain a smooth surface and a tight fit. The bearing would be kept in place by a grub screw gently pressing against the outer ring.
Using a piece of aluminum scrap we were able to test this arrangement.
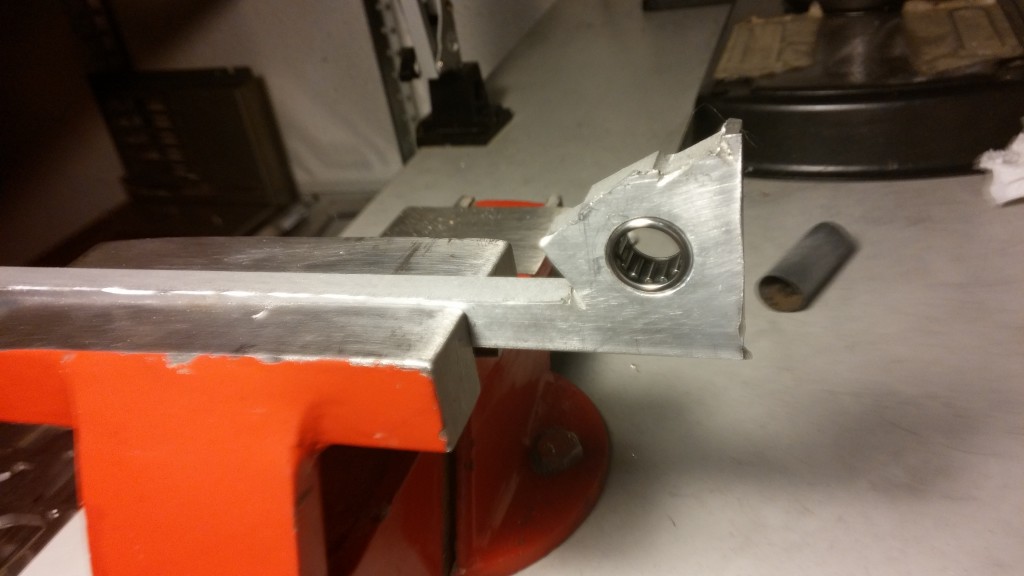
The rear bearing housing required some more thought. This bearing would support the axial load exerted by the end effector pressing perpendicularly to the equipment panel and would have to be properly fixed to counter this load. This meant that the housing would have two concentric holes: one trough the whole part with a 14mm diameter and another only half way with a 16mm diameter.
Machining a new part from scratch would make it easy to accurately cut this feature into the part, while machining the existing part would make it nearly impossible to align the part with the needed accuracy.
A third option was selected: drill a second 16mm hole halfway over the previously drilled 14mm hole. Using a drill with a 135º split point meant that instead of having an “horizontal” bearing surface we would have instead a truncated conical surface with a 22.5º inclination towards the center. While this might not be the ideal surface to support the bearing, the modest axial loads would still be under the values needed to start deforming the housing.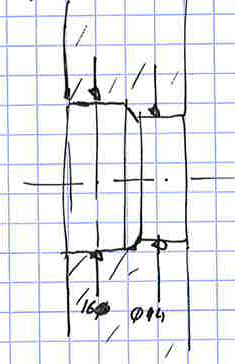
The two aluminum parts had to be carefully aligned and drilled in a single operation. This was further complicated by the fact that one of the parts already has three binding post screws protruding from it. 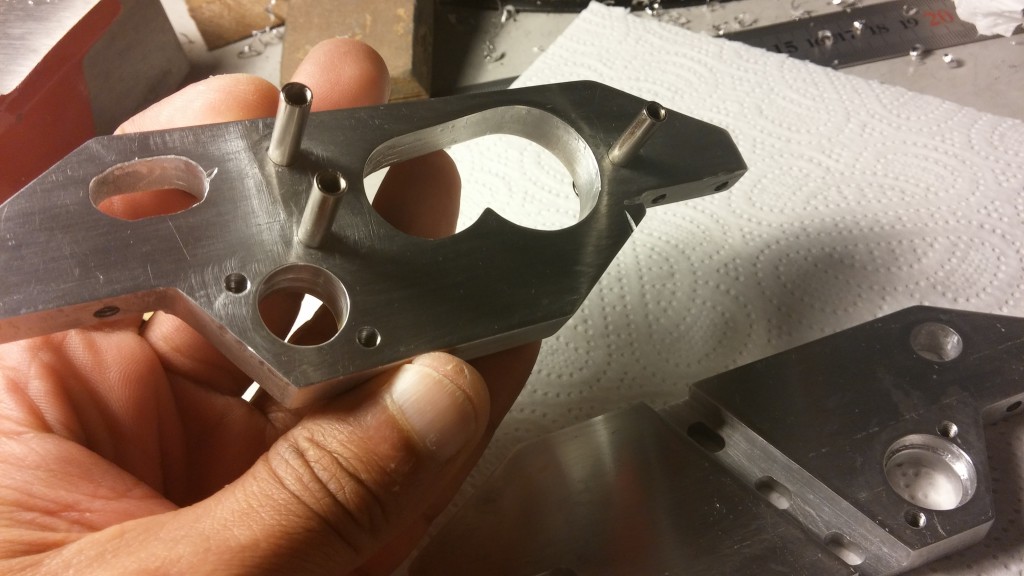
So a complicated fixing jig had to be arranged for this operation.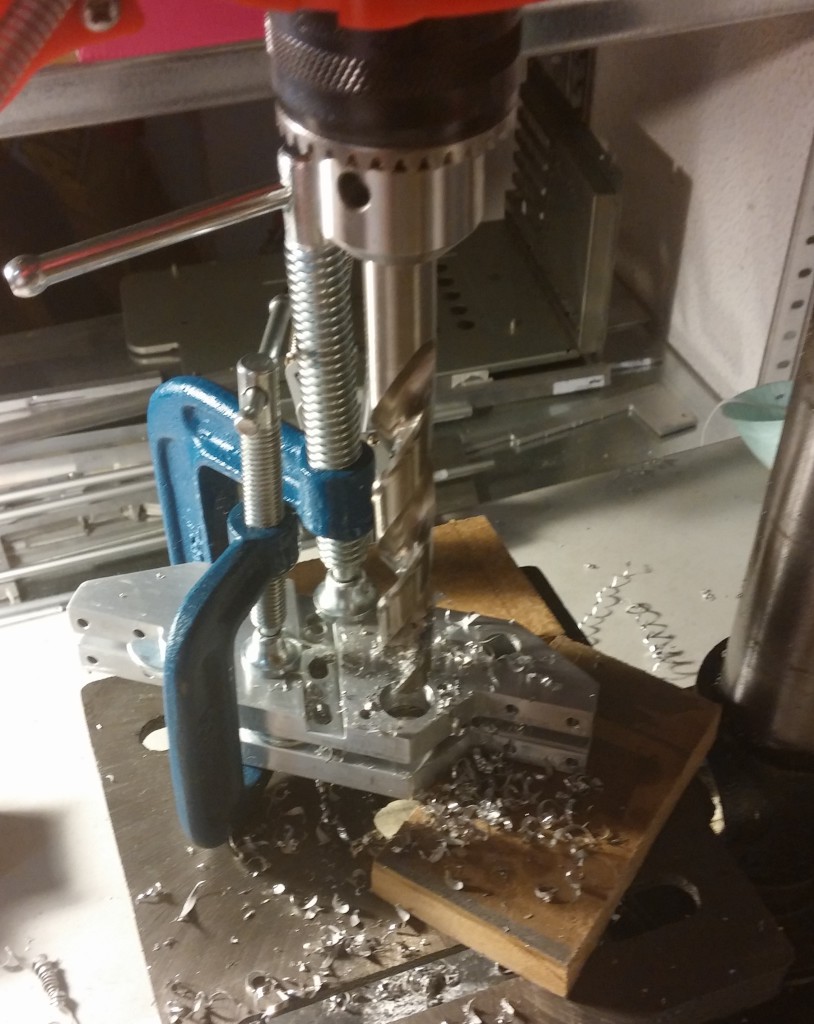
Finally we got the two parts ready to house the bearings.
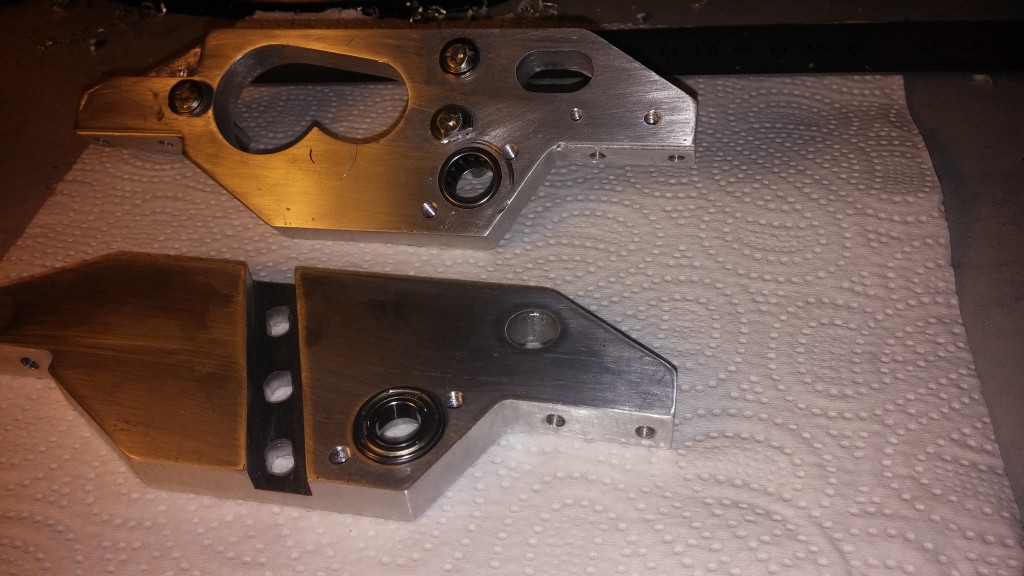
We machined an additional part which presses over the bearing and keeps it in place while resisting the main axial load.
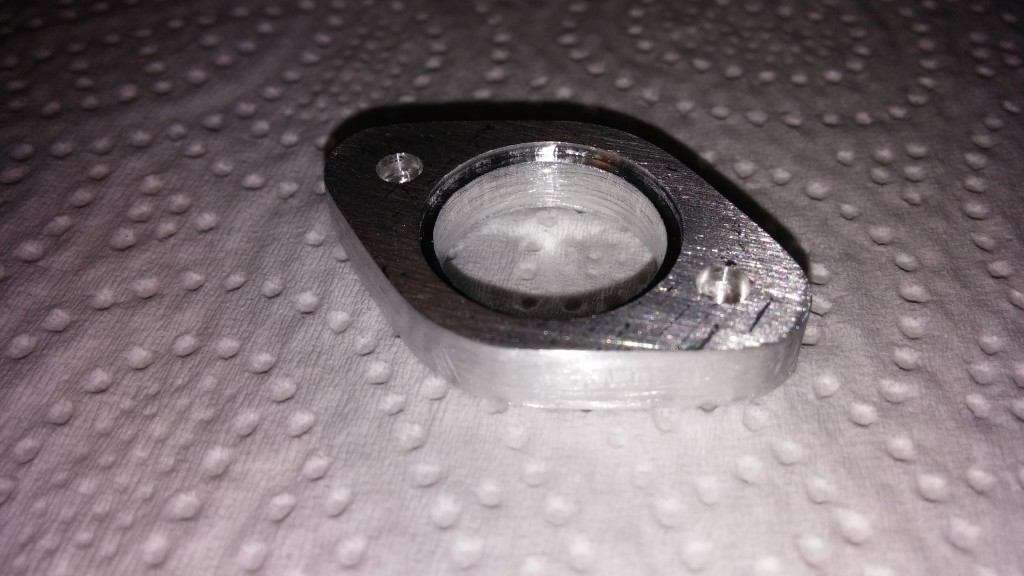
We then set up the assembly using the temporary aluminum shaft built with our DYI combined milling/Lathe machine.

Even with this temporary shaft and a damaged bearing (damaged during installation) we could immediately notice the improvement from using proper bearings.